Five-Axis Medical Component Facility From Hemlock Engineering
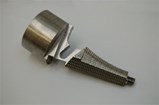
Kent, U.K. - A single cycle machining strategy for producing complex medical components is being offered by Hemlock Engineering using the latest five-axis machining centre technology supported by 3-D solid model CAD to CAM for creation of true continuous five-axis milling.
Explains Paul Cobb managing director: "Having installed the two Mikron XSM 600U five-axis vertical machining centres both with seven pallet systems and 60 tool magazines, we are able to provide continuous production and batchwork machining from solid and approach five or sometimes 5½ faces of a component in a single fully automated cycle."
Having invested more than £1M in its five-axis machining facility that employs 36 people, Paul Cobb has set up a true design for production consultancy working direct from solid models. Leading the consultancy is 3-D machining specialist Nick Marks, with a brief to provide a service to customers' design and development teams to reduce costs and help improve functionality of the machined parts required.
Hemlock Engineering has the latest version of Open Minds HyperMILL/HyperCAD GSM software as well as SolidWorks and SolidCAM programming software that enables any part to be processed from CAD to assembly. By installing a Mitutoyo Crysta Apex C574 co-ordinate measuring machine with Renishaw P410 probe, parts can be reverse engineered through Cosmos 3 software.
Both Mikron XSM 600U machines are fitted with high speed 36,000 revs/min spindles and are capable of 90 m/min rapid traverse rates. The in-built rigidity of the machines enable both free cutting aluminium and high grade steels, typical of the medical industry, to be very effectively machined. The five-axis Mikron machines are part of the Hemlock Engineering facility that has 17 three and four-axis vertical machining centres with high productivity multi-vice and zero-point high accuracy fixturing set ups.
The machines have linear drives fitted to each of their five axes and the rotary table is able to spin at up to 300 revs/min. Because of the configuration of the machine specified by Paul Cobb, milling, drilling, boring and turning can be performed as part of the same cycle. And with the 60 tool magazine and seven pallets, the machines can be set to run batches of parts in unmanned automatic cycles thus reducing lead time and operator dependence.
SOURCE: Hemlock Engineering Ltd.